Matthew J Poes
AV Addict
- Joined
- Oct 18, 2017
- Posts
- 1,904
It's been a while since I've updated this thread with our progress. That's mostly because there hasn't been much progress
I am currently pulling speaker wire in the theater. I decided to also run conduit to all speaker locations, and for subwoofer cables and of course video cable to the projector location. Hopefully I can get the conduit installed this weekend.
I investigated the possibility of doing a minisplit HVAC system for the theater. I found some rather quiet ones (around 20 dBA). Unfortunately, the installed price of these units tops $3000. Considering that we're already over budget on this add-on, we are not too keen on spending that much more. It turns out I don't have enough room for a dead vent, without stealing non-negotiable space from the adjacent room. Long story short, the theater will share HVAC with the rest of the house. I am now looking for inline silencers for the theater supply and return trunks to minimize airborne sound transfer through the ductwork.
My primary concerns with tying the theater HVAC into the rest of the house are: 1. Sound transfer via the ductwork (airborne and breakout noise), which I think I can minimize with careful planning; 2. The potential for the theater to need to be cooled when the rest of the house needs to be heated. Since the theater will be insulated on all sides, and there will be equipment in the room and sometimes several people, it could get quite warm in there while the rest of the house is too cool. I can close the vents in the theater, but that may not be enough and will also introduce air turbulence noise when the HVAC system is running. Perhaps I will have them install a damper ahead of the theater trunk that can be separately controlled.
I suppose if it turns out to be a big problem, I could have a minisplit installed in the future when the bank account recovers.
Anyway, there's the latest for ya.
Having gone down a similar road I can give you all the information on what I did, but I'll warn you up front that silencing ducting is expensive. What I found out was that you need to look for deals and even into custom fabrication as a means to keep costs down. This will all be a balancing act, as perfect is just too expensive to be realistic.
Tidbits on Soundproof Ductwork:
- Steels ductwork provides similar sound isolation to 1/2" drywall, but resonates significantly and at the resonance frequency allows a great deal of sound to penetrate.
- Flex duct does not provide any significant sound isolation, nearly all sound that enters flex duct escapes, known as break out noise. Acoustic Flex duct's only advantages to steel ductwork is that sound does not travel down/through the length of the duct and provides physical isolation between the theater and main trunk. Remember that the main reasons that sound doesn't travel down the duct is not just that it absorbs, its also because most of the sound simply escapes. That is important because if you forget that, its easy to install it in a way where it defeats your soundproofing.
- https://www.acrytech.com/product/acoust-x-sound-damping-coating-5-gallons/ this product provides good damping at a good price for steel ductwork. I used it inside and out on the ductwork near and inside my theater.
- http://www.jm.com/en/building-materials/hvac-insulation/duct-liner/spiracoustic-plus/ this is the product I used to line my ducts. While duct silencers are good, most of them operate on a principle of absorption over distance and a velocity change via an expansion chamber. What this means is that they aren't special and can be recreated easily. You can equal a 24" long Duct for 6" ducting by simply buying a piece of 24" long duct material that is 9" to 10" in diameter and lining it with 1.5" insulation. Then using reducers on each end. This isn't cheaper if all you do is one 24" duct. The real issue is that the decibel loss is very small, so you need more than 24". Custom lets you make much larger ducts. For example, I would go with 8" instead of 6" and I would increase the size to something like 14" duct for the muffler lined with 2" material, and make it much longer, like 6 feet long if possible. An ideal scenario would have a total of ten feet of absorption or more for each supply and each return. This stuff is expensive so look around and ask for discounts. Don't go to big box stores, they won't have and if they do, the price is unlikely to be good. I got a good deal by buying a damaged roll.
- Spiral duct is better than snap together round duct, and round duct is much better than square duct. Spiral duct is normally a higher gauge of steel which provides more absorption and its stiffer so it contains low frequencies better. This has been researched and shown to be true, so its a practice worth following. Unforutnately that means you need to use commercial duct in a non-commercial scenario, so price goes up. Again, ask for deals and scraps. I was able to mix commercial and non-commercial products in key ways to save money. Everything into the theater is commercial, everything outside of the theater (after a few feet) is domestic. I also used a acoustic lined specialty product for the long runs in addition to my mufflers, which I don't suggest. It's the same thing as I created and was pretty expensive.
- Fancier and more effective mufflers exist, it may be worth pricing them out, but...I found they were as expensive as a split system. A muffler could be $1500 or more. They are almost always custom. It is possible someone will have created one for a customer that the customer didn't use, so you might find a deal.
- Expansion chambers are good to reduce air noise, but should not be too close to the return and supply exits. I don't know what best practice is, might want to consult a professional. Just know that most HVAC companies do not really understand sound and acoustics, so I got mixed information. I contacted a company that specializes in HVAC for large buildings and studios.
- Expansion chambers with offset entry and exit are better, in general reducing line of sight type scenarios are good, you want the air to have to change direction, but it also needs a surface to absorb on as much as possible.
- 90 degree bends or any sharp change in direction is good for sound in some ways and bad for sound in others. The indirect path helps more sound to be absorbed by encouraging more reflections and thus more sound hitting the absorption material. The bad is that it causes air turbulence and increase low frequency noise. Turning vanes fix this and acoustic turning vanes are ideal. The problem is they are expensive. If you are more adventurous than I, you can buy prefabricated turning vanes and install them in a custom made expansion box on your own. You might also just ask a local fabricator what the cost is, it might not be bad. The quotes I got were very high.
- Metal ductwork will transmit sound directly through the metal itself. It vibrates and reradiates the sound. The solution is two fold. One is the damping of the metal (which I did). The other is the inclusion of one or more flexible connections. I didn't do this because I worried it would let sound out. It turns out the flexible vibration break is too important. I should have done it.
- Lower air velocity makes less noise. Larger ductwork reduces air velocity. Changes in the duct area to a drastically larger one also lowers velocity (so if you then reduce it again, the velocity doesn't increase as much as the velocity before the expansion).
I'm looking at building additional soffits near my ducts that will cover the ducts and be lined with Ductboard. This will create and indirect entry to the duct and provide a lot of sound absorbing surface, as well as a large in room expansion box. While I said earlier expansion boxes shouldn't be close to the exit, what I found is that there are two ways these are done. One is an expansion box in the traditional sense. Because of the offset entry and exit, they can cause noisy turbulence. The other is more of a giant flare, and this kind of expansion box does the opposite, it doesn't create turbulence and actually reduce airflow sound. Here is an example:
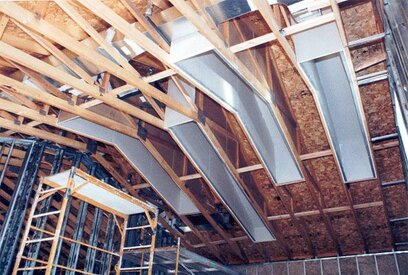
When I get a chance, I can share drawings of my idea, which is similar to this, but creates a more indirect path for the air to travel.
Oh one last thing, pick your vent covers carefully. Vent covers can generate noise. A number of people complain about this. My solution was to reduce air velocity as much as possible. None the less, I do find the vents add a little noise. Linear vents are more aerodynamic and work best, but they are really expensive. If you find a cheap solution let me know. I don't have one myself.